How Do I Choose a Motor?
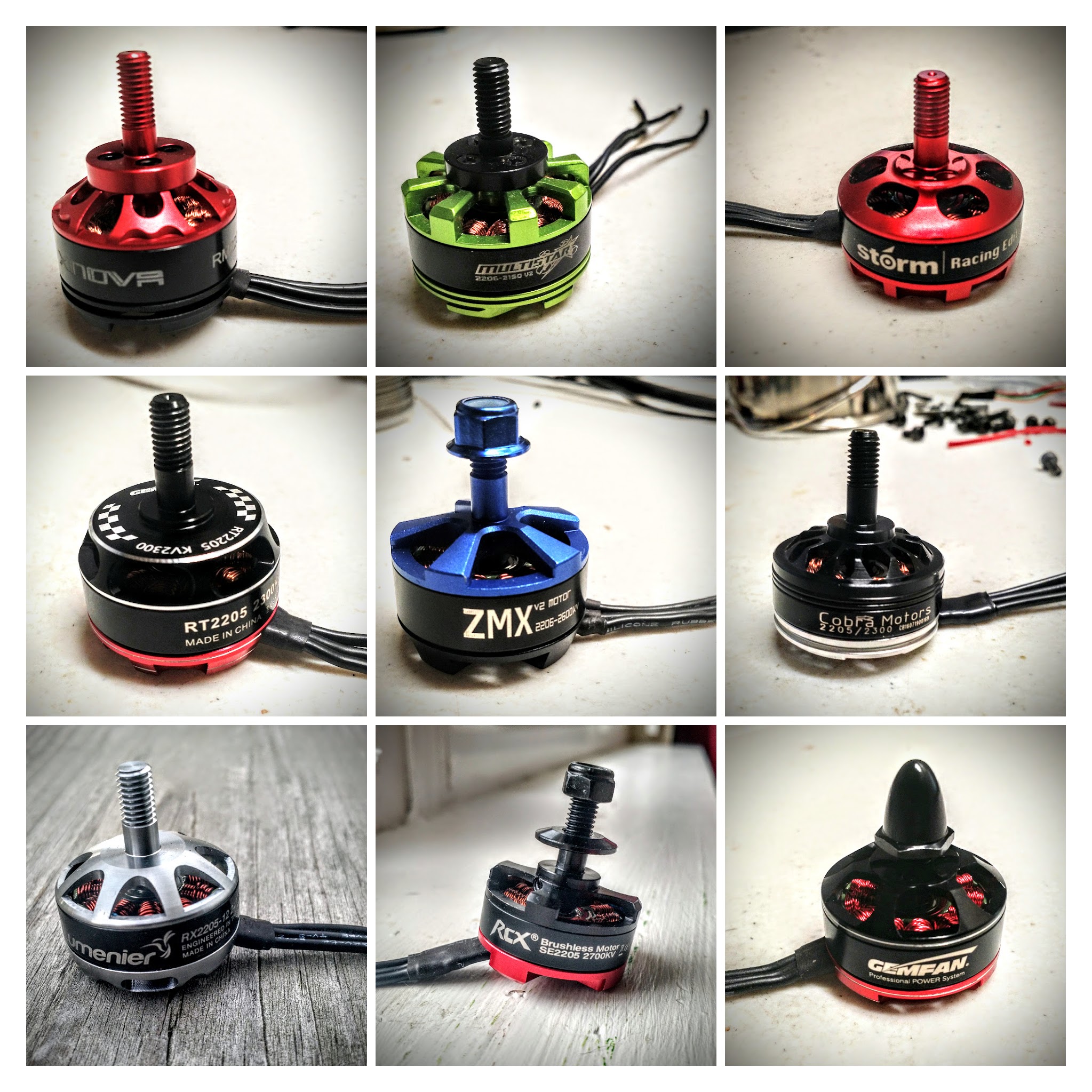
With the plethora of motors out there, the question of how to choose a motor that is right for you becomes ever more important. One of the most frequent questions I get asked is "what is the best motor?" and like so many other questions I get, my primary answer is "it depends!" I will try make a more thorough explanation here of how to make a choice that will be best for you, as well as explain how to read the motor test results in a way that will give the answers needed.
Identifying Considerations
The first thing we really need to do is analyze what we want out of a motor, and what considerations are important to us personally. To do that, we need to understand what factors impact motor performance and how they translate into in-flight performance, as well as how these factors influence each other. Many of these considerations operate on a spectrum and finding the right motor for our needs is mostly identifying where on the spectrum our flying style fits. In the end we must weigh all the factors in a motor's performance to decide if it will be the "best" motor for our particular application.
The considerations we need to take into account can be broken down into several categories: weight, power, efficiency, and response/torque. In some ways these are inter-related, but they have distinct impacts on how a quadcopter will handle in the air. Let's take a closer look at each of these and how they will impact what we can feel in flight.
Motor Weight (Moment of Inertia)
Motor weight is an easily overlooked factor when choosing a motor. The rationale is typically "Motor X weighs 5g more than motor Y, but motor X generates 100g more thrust, so it more than compensates." There are few problems with this statement that make it an incomplete picture of the impact of motor weight in the air. The primary issue with this line of thought is that we're not just dealing with linear acceleration on a quadcopter. Much of what we do in the air comes in the form of angular acceleration. Angular acceleration is impacted largely by a factor called Angular Momentum or Moment of Inertia. This calculation doesn't actually take thrust into account at all, basically defining how much the object will resist changing speeds of angular rotation.
In this case the two variables we care about are mass and radius. The formula being I (moment) = mass x radius squared, means the further from the center of ration and the more mass, the more the object will resist changing speed of angular rotation. Essentially a heavy motor will require more torque (not just thrust, we'll cover that momentarily), and as a result more time to accelerate and decelerate to the desired speed of rotation. In practical application this means the quad will feel less precise in the air, and the PID controller will have to work harder to get the quad turning when starting a flip or a roll, and then to stop it turning at the end. Some of this can be compensated by tuning, but in the end, a lighter motor will typically "feel" better and more precise than a heavier motor, given that all other elements are equal. Boiling this down to essentials, if our flight style involves lots of acrobatics and fast changes in direction, the weight of the motor will matter more to us than if we're primarily interested in going really fast in a straight line.
Motor Mechanical Power (RPM/Thrust)
The impact of power is one of the most directly applicable and straight-forward aspects of motor performance, and probably the one that is most often observed. I would argue however that in most instances it's not as important as some of the other factors we're going to discuss. Power is primarily an indicator of the top end maximum output of RPMs/Thrust of a motor. In relation to itself though, it is hard to measure the real impact of this. It primarily needs to be considered in conjunction with the other elements we're examining, or other factors altogether. The biggest impact of maximum output power, or even output power across the throttle range, is in relation to the total flying weight (All-Up-Weight or AUW) of your quad. A heavier quad will need a higher power motor to really fly well, and the lighter the quad, the more positive difference the output power makes in terms of handling.
Essentially a fairly weak motor in terms of RPM output on a very light quad may handle better and feel better in the air than a heavy quad with powerful motors. Knowing your planned all up weight, is an important factor in choosing an appropriate motor. The common term referred to is the power-to-weight ratio. This is typically calculated by the maximum static load output of the motors multiplied by the number of motors and divided by the AUW of the quad. There are a couple of reasons why this is also an incomplete picture of performance. Maximum thrust numbers are a static measurement, and in practical terms have very little bearing in a dynamically loaded environment, like flight, by themselves. That being said, there is still significance, as a motor that has a higher RPM output and a higher thrust output in flight will typically perform better. What we really want to look at is a combination of the typical power to weight ratio, and the pitch speed of the motor/prop combination we are considering. Pitch speed is calculated by the RPMs of a given propeller multiplied by the propeller pitch angle, to give us an idea of how much forward motion a propeller will be generating in a dynamic environment. Again this is not a perfect assessment due to efficiency losses and other factors like Effective Angle of Attack, but it gives us a good idea when combined with our traditional power-to-weight ratio of how the maximum forward speed our air-frame will be capable of reaching, as well as how fast punch-outs on the quad will be at maximum throttle.
Motor Efficiency (Electrical Power vs Mechanical Power)
This factor is closely related to the previous factor we examined, but is impacted by a number of other factors. In this consideration, it is really very much a spectrum in relation to the maximum mechanical power vs. the best efficiency. There is a balance to be struck between what our needs are for top end, and how much we like our batteries. Ideally a motor would be both insanely powerful and sip battery power, but we haven't quite gotten there yet. For some, efficiency will be more critical than others depending on flying style and goals. When looking all of the factors together, it is possible to have a very well handling quad that doesn't abuse the batteries, but it comes at the cost of top end performance in terms of wide-open throttle (WOT) forward flight and punch-out speed. Also we will want to consider voltage sag as part of this factor, given that a more efficient motor will cause much less of a voltage drop across the battery, resulting in a higher running voltage and less of an RPM loss than might otherwise be considered.
Another aspect of this factor (and this one is easy to forget) is that efficiency isn't only about the very top end of the throttle. Many of the new high strength motors out are actually more efficient than their counterparts when comparing the same thrust output, they just have a higher top-end which means a higher total draw. Motors also will typically lose a bit of efficiency as they approach the limits at the top end, so a more powerful motor may show a lower efficiency rating in terms of grams per watt at a given throttle percentage, but may actually be MORE efficient in terms of grams per amp at an equivalent thrust output. This is where our flying style plays a major role again when considering efficiency. How much time is spent at WOT, and how carefully we want to guard our WOT usage will impact drastically how we consider efficiency in our motor choice.
Motor Torque (Response Time)
One of the least considered and (in my opinion) most significant factors in motor choice is actually the torque a motor is capable of producing. It is hard to under-estimate the impact this has on how a quad handles in the air. Torque impacts how quickly a given propeller is capable of achieving a given RPM. This has a tremendous impact on the PID controller's ability to make fast changes to the system, greatly impacting the ease of tuning, as well as the angular acceleration and precision of the quad on flips and rolls.
The most significant indicator of torque is stator size, so in some ways this factor is a spectrum between response times and motor weight. However the recent batch of high powered motors driven be newer generations of magnets, and advances like arc magnets, narrowing air-gaps between the magnets and stators, and 0.15mm stator laminations, are all driving up the torque capacity of smaller, lighter class motors. The motor torque not only plays a role in motor choice, but also prop choice. This really requires us to examine closely both the motor and prop choice in combination as we examine different options. A light weight prop (in terms of loading and moment of inertia, not necessarily physical weight) will respond significantly faster to RPM changes than a heavier prop. This fact largely explains the long popularity of the 5x4x3 propeller, as the balance between thrust output, rpms, and the speed at which it reaches RPMs is optimal for certain types of flying, namely freestyle and acrobatics. Again this factor may not make much difference in terms of fast straight flight, but in terms of acrobatics and tight proximity work, as well as the precision and quality of the tune, torque is a major contributing factor.
But what about KV!?
I'm sure you've been reading so far and shouting at this at the screen the whole time! The truth is that KV (like stator size and prop choice) is only impactful in terms of how it balances the factors mentioned above. A motor KV will impact top RPMs, and what prop you need to choose to get the best efficiency an best response times. Lower KV will push heavier props with less current draw and faster response times, where higher KV is more suited for lighter props at the cost of efficiency, but gaining RPMs. What KV will be best suited for our flying style depends on a combination of prop choice and flying style, as well as stator size. KV is like a final fine tuning of all the choices that makes everything work together optimally. In my opinion it is best practice to decide how important all the other factors are for your application, and then choose the KV, prop selection and stator size to fill those needs.
Reading the Data
So we now know what factors play a role and how they impact our flying style, so how do we know if a motor will fill our needs? Reading the data and looking closely at the information can be challenging if we don't know where to look. So how do we identify the factors listed above in the data? Weight is simply a number, so nothing difficult there. Power and efficiency are fairly self explanatory, simply looking at the thrust data gives our power readings, but when running comparisons it is very helpful to look at not only the maximum thrust at 100% throttle, but also compare the numbers at all throttle points and the ramp graphs. Comparing between the data in the tables in the results spreadsheets gives a fairly good idea on relative efficiency and power and rpm values, but judging the other aspects and directly comparing two or more motors becomes increasingly difficult. The last graph on the Motor Data Explorer page was specifically designed for this as well examining the response times and torque between motors, which is nearly impossible to tell from looking at the numbers alone. Lets examine a few graphs from that chart to give us a better idea of what we're looking at.
In this graph we're seeing a selection of motors from the data set that represents a pretty good variance of what have been considered the higher performers over time. What we're looking at is a 300ms time slice right after the command to go from idle throttle to 100% throttle. This is the best way of assessing response time between motors, as it represents the most demanding situation a motor can be asked to handle, but it also show relative maximum thrust values at the instantaneous transition point. A couple of things jump out at us here, primarily just how much things have improved in the last 6 months to a year! Lets break this chart down though.
In this example there are two variances we care about related to the two axes of this graph. The vertical axis is thrust output, and the horizontal axis is time. This translates into a gap in performance between motors that is clearly visible between lines on the graph. Here we see a gap in thrust output at the top and a gap response time performance to the left. In terms of response times the steeper the slope the better, and the less of a "tail" or slope on the settling side the better. For thrust clearly the higher the number the better. You can see that motor choice has a significant impact on the acceleration time.
By selecting the 24ms time range and refreshing the graph we can take a look at the braking sequence from 100% to idle. You can see here that all the motors brake at essentially the same speed with this prop. However, notice the huge variance just changing props makes, with the Cobra 2300kv on the 5x4.6BN prop. This clearly demonstrates that prop choice has much larger impact on braking speed than motor choice, while motor choice has a more significant impact on acceleration speeds. This is why it is important to run the comparisons on several props that you might be thinking of running with each motor choice.
By selecting amps and volts as the metrics, and reloading the graph, we can also get a look at comparative efficiency at the given sequence as well. Here the vertical axis contains two scales one for each metric, and the horizontal time scale is fairly irrelevant. Remember when comparing these metrics (as well as peak thrust) to compare across all the time ranges mentioned above the graph, as you may see some significant variance across the throttle ranges and the ramp.
Conclusions
What motor is the "best" motor is a highly personal choice based on the needs of the pilot and preferred flying styles. Identifying the priority of the factors discussed here will help you choose the best motor for you and your needs. Hopefully this discussion has helped you identify those factors that are important to you and make an informed decision for your next build.